The new Linea2 4k color camera with a 5GigE interface delivers RGB images at a max line rate of 42kHz x3. That’s 5x the bandwidth of the popular Linea 1 GigE cameras.

Perhaps you already use the Linea GigE cameras, at 1 GigE, and seek an upgrade path to higher performance in an existing application. Or you may have a new application for which Linea2 performance is the right fit. Either way, Linea2 builds on the foundation of Teledyne DALSA’s Linea family.
Why line scan?
While area scan is the right fit for certain applications, compare area scan to line scan for the hypothetical application illustrated below:
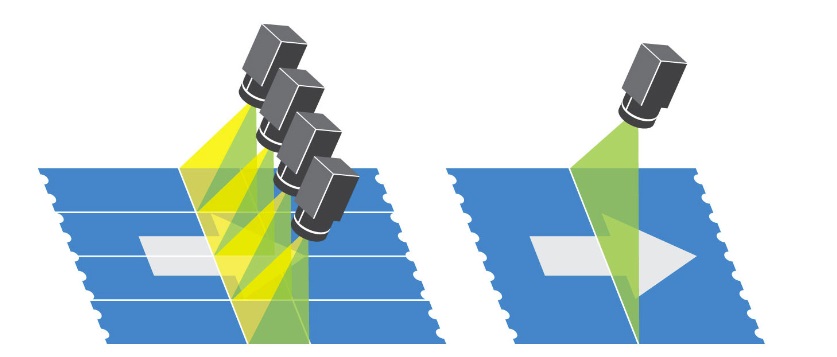
If one were to implement an area scan solution, you’d need multiple cameras to cover the field of view (FOV). Plus you’d have to manage lighting and framerate to avoid smear and frame overlaps. With line scan, one gets high resolution without smear, and a single camera solution – ideal to inspect a moving surface.
Call us at 978-474-0044 to tell us about your application, and we can guide you to a suitable line scan or area scan camera for your solution. Of course we also have the right lenses, lighting, and other components.
Sensor
The Trilinear CMOS line scan sensor is Teledyne’s own 4k color design, with outstanding spectral responsivity as shown below:
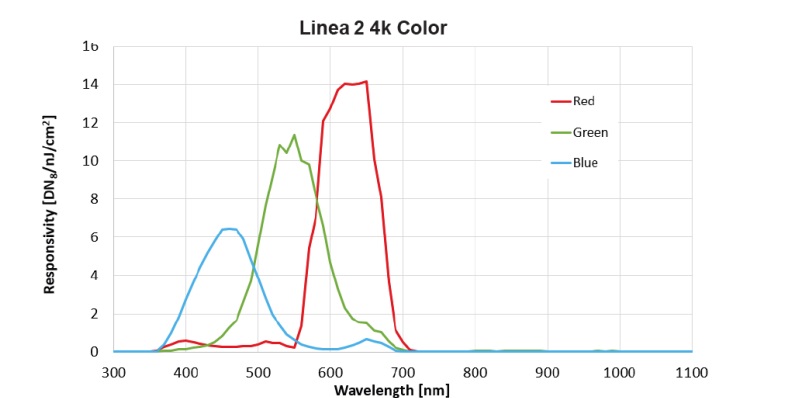
The integrated IR-cut filters insure true-color response is delivered on the native RGB data outputs.
Interface
With a 5GigE Vision interface, the Linea2 provides 5x the bandwidth of the conventional GigE interface, but can use the same Cat5e or Cat6 network cables – and does not require a frame grabber.
Software
Sapera LT software development kit is recommended, featuring:
- Intuitive CamExpert graphical user interface for configuration and setup
- Trigger-To-Image Reliability tool (T2IR) for system monitoring
Sapera LT has over 500,000 installations worldwide. Thanks to the 5GigE Vision interface, popular third party software is of course also compatible.
Applications
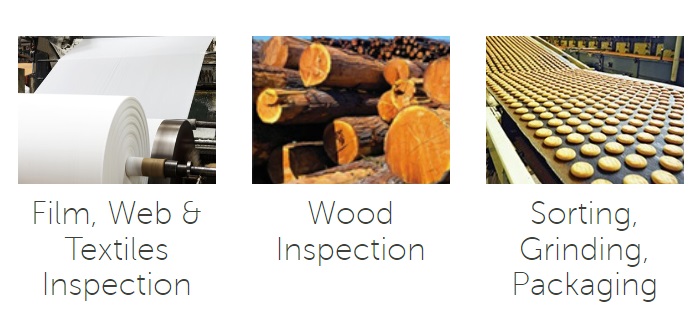
While not limited to those listed below, known and suggested uses include:
- Printing inspection
- Web inspection
- Food, recycling, and material sorting
- Printed circuit board inspection
- Web inspection
- etc.
Call us at 978-474-0044. Or follow the contact us link below to provide your information, and we’ll call you.
1st Vision’s sales engineers have over 100 years of combined experience to assist in your camera and components selection. With a large portfolio of lenses, cables, NIC cards and industrial computers, we can provide a full vision solution!